Making Acetel Fast travel ACME tap (3/8"-8 with 4 starts)
A quick search of the internet will show people making their own taps with a rotary tool and a grinding wheel. For standard lead taps this method works fairly well. I use an end mill with a larger radius bit to cut the flutes, but the principle is the same. Fast travel nuts can be troublesome. It is difficult to get a decent bite before there is enough force to pull the tap deeper. The solution to this problem is to ensure that the tap is moving into the acetal nut at the correct rate. For a 3/8"-8 with 4 starts, the tap needs to move 1/2" per revolution of the tap. The method I use is to use a 660 bronze nut in an aluminum frame. The acetal nut (white in the picture) is pushed against the aluminum frame and has pins in the slots to keep it from rotating. With a sharp cutting edge on the tap, the effort to hand cut the treads is manageable. The tap itself is a 2 flute design with an 8 degree rake angle. The last 1.25 inches is tapered about 6 degrees.
There are 2 common ways of removing backlash. The first is to clamp radially, the second is to clamp axially. There is a good bit of information online on both methods; I prefer the second method. I plan to use 2 nuts per ACME rod snugged against one another to axially remove the back lash. This means there will need to be 2 nuts on each ACME rods. This method allows for adjustment with wear. I will write an article on this design in a later blog.
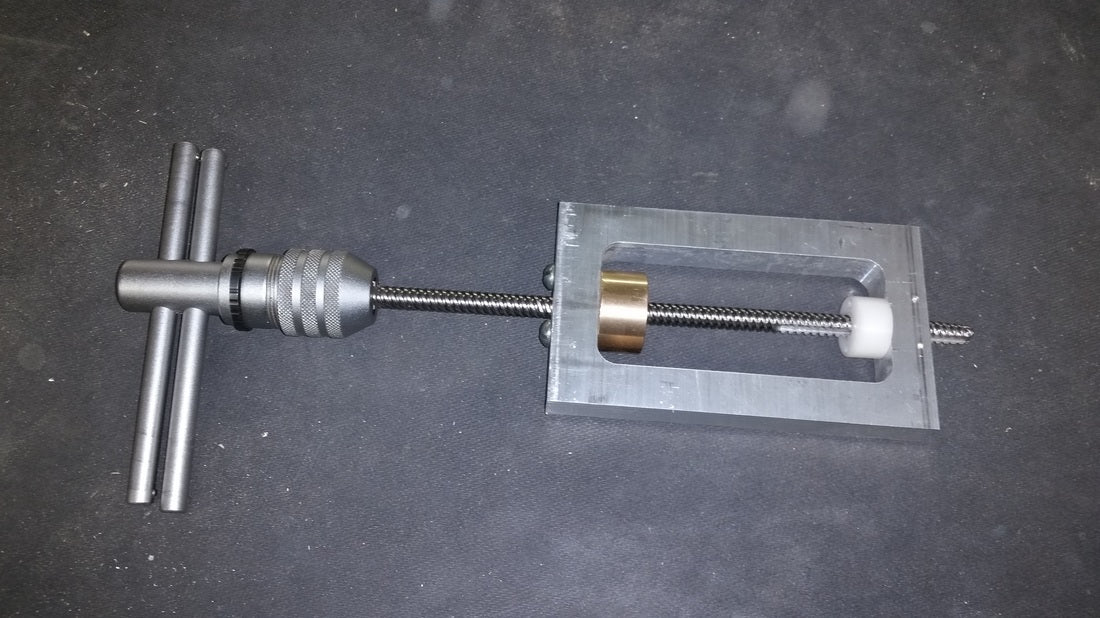
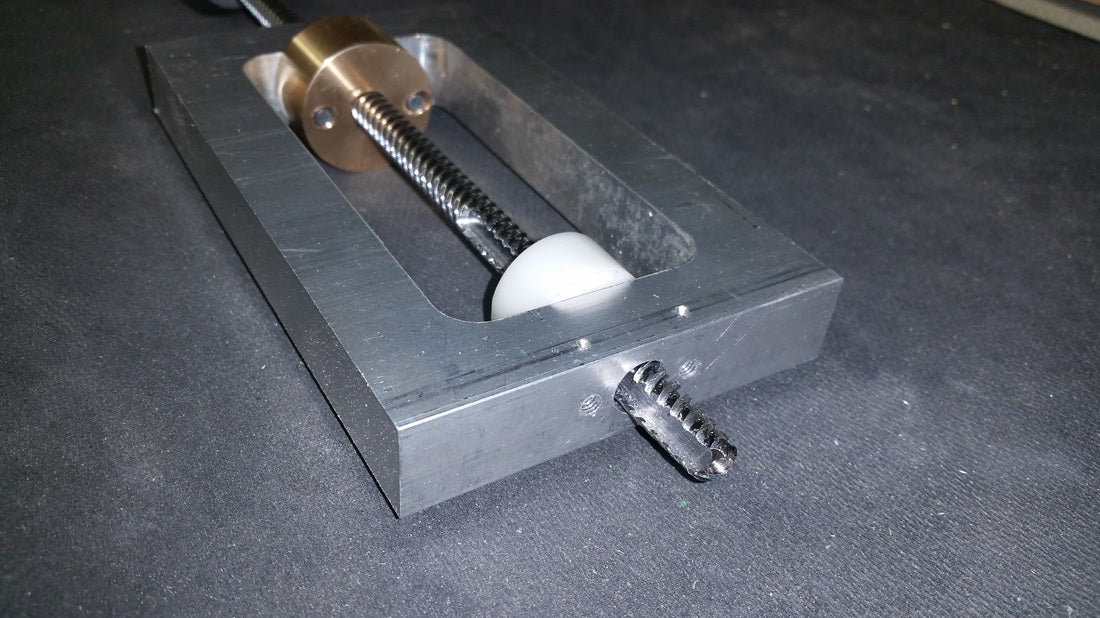